The Essential Guide to Injected Molded Plastic in Metal Fabrication
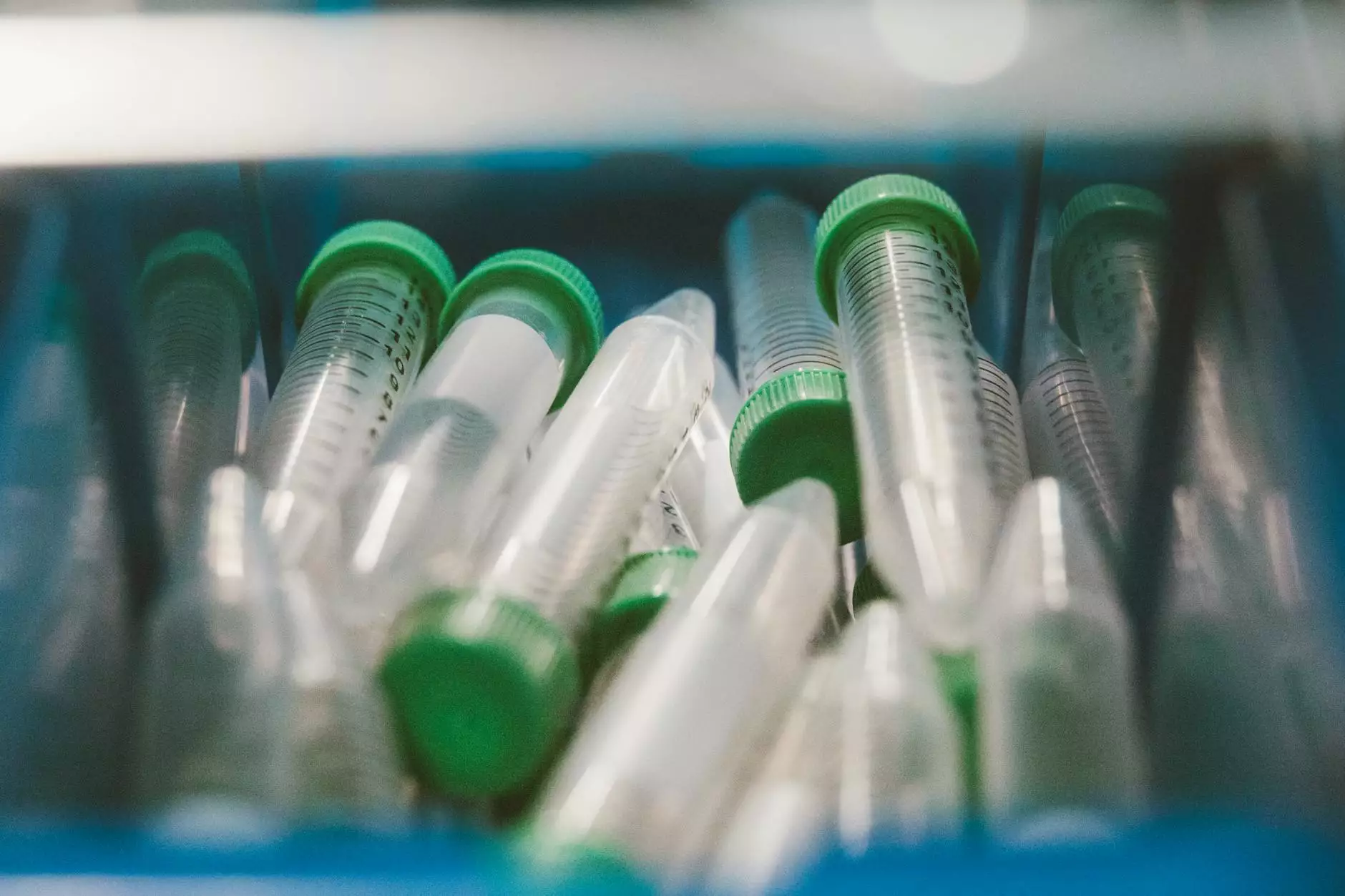
Injected molded plastic is rapidly becoming a cornerstone in modern manufacturing, particularly in the domain of metal fabrication. This comprehensive article explores the methods, advantages, and applications of injected molded plastic, especially within the context of the metal fabrication industry.
Understanding Injected Molded Plastic
Injected molding is a manufacturing process for producing parts by injecting molten material into a mold. This technique is versatile, enabling the production of complex shapes with high precision. The process typically involves several key stages:
- Material Selection: The process begins with selecting the appropriate plastic material. Common choices include ABS, polypropylene, and nylon.
- Melting: The plastic pellets are heated until they melt into a viscous liquid.
- Injection: The molten plastic is then injected into a mold under high pressure.
- Cooling: Once the plastic fills the mold, it is allowed to cool and solidify.
- Ejection: After cooling, the newly formed plastic part is ejected from the mold.
This process offers significant advantages over traditional manufacturing methods, especially in terms of efficiency and design flexibility.
The Advantages of Injected Molded Plastic
Implemented in metal fabrication, injected molded plastic presents several benefits that can propel businesses into a competitive position:
- Cost Efficiency: The reduced material waste and accelerated production cycles lead to lower costs per unit.
- Complex Designs: The ability to create intricate shapes and designs is unmatched, allowing for more creativity in product development.
- Consistent Quality: Injection molding offers high precision and repeatability, minimizing defects and assembly costs.
- Material Variety: A wide range of plastic materials can be used, each with unique properties, such as flexibility, strength, and resistance to heat and chemicals.
- Environmental Impact: Many modern injected molded plastics are recyclable, which is a crucial consideration for eco-conscious companies.
Applications of Injected Molded Plastic in Metal Fabrication
The versatility of injected molded plastic extends to various applications in metal fabrication:
1. Components and Parts Manufacturing
Many industries rely on the production of plastic components that integrate seamlessly with metal parts. For instance, in the automotive sector, injected molded plastic is used for producing dashboards, panels, and connectors that complement metal assemblies.
2. Tooling Solutions
Injection molding creates durable tooling solutions, such as jigs and fixtures, that improve the accuracy of metal fabrication processes. These tools enhance the reliability and precision of metal working activities.
3. Consumer Products
Many consumer goods incorporate both metal and injected molded plastic components. From electronics to household items, the combination allows for lightweight, durable products that appeal to consumers' needs.
Challenges in Injected Molded Plastic
Despite its numerous benefits, there are some challenges associated with using injected molded plastic in metal fabrication:
- Initial Costs: The setup costs for injection molding can be high due to mold design and machinery investment.
- Material Limitations: While plastic offers great versatility, some applications may require properties that exceed what current plastic materials can provide.
- Design Constraints: Designing for injection molding requires careful consideration of draft angles and wall thickness, which can limit creative options.
Choosing the Right Partner for Injected Molded Plastic Solutions
When selecting a manufacturing partner for injected molded plastic solutions, consider the following criteria:
- Experience and Expertise: Look for companies with a proven track record in both injection molding and metal fabrication.
- Technological Capabilities: Ensure they have the latest machinery and technology to support high-quality production.
- Material Knowledge: A deep understanding of material properties and how they interact with metal components is crucial.
- Quality Assurance: The company should employ rigorous quality control measures to ensure consistency and reliability.
- Environmental Practices: As sustainability becomes increasingly important, ensure that your partner is committed to environmentally-friendly practices.
The Future of Injected Molded Plastic in Metal Fabrication
The future of injected molded plastic in the metal fabrication industry is promising. Emerging technologies such as 3D printing and advanced robotics are reshaping this field, potentially enhancing the precision and possibilities of ripped molded plastic integration.
As manufacturers continue to explore hybrid materials and innovative processes, we can expect injected molded plastic to play an even more substantial role in the advancement of metal fabrication techniques. The synergy between metal and plastic will unlock new possibilities in product design and functionality.
Conclusion
In conclusion, the implications of injected molded plastic in the metal fabrication sector are profound and far-reaching. It offers a unique combination of cost-effectiveness, design flexibility, and environmental sustainability. As the industry evolves, so too will the applications and technologies surrounding this innovative manufacturing process, ensuring it remains at the forefront of modern production.
Whether you are a manufacturer, designer, or engineer, understanding and leveraging the benefits of injected molded plastic can dramatically enhance your product offerings and operational effectiveness in the ever-changing landscape of manufacturing.
Contact DeepMould for Expert Solutions
If you’re looking to incorporate injected molded plastic into your metal fabrication processes, consider partnering with DeepMould. Our team of experts is ready to assist you in achieving your manufacturing goals with cutting-edge technology and unparalleled expertise.