Driving Innovation and Efficiency with Rapid Prototyping Injection Molding
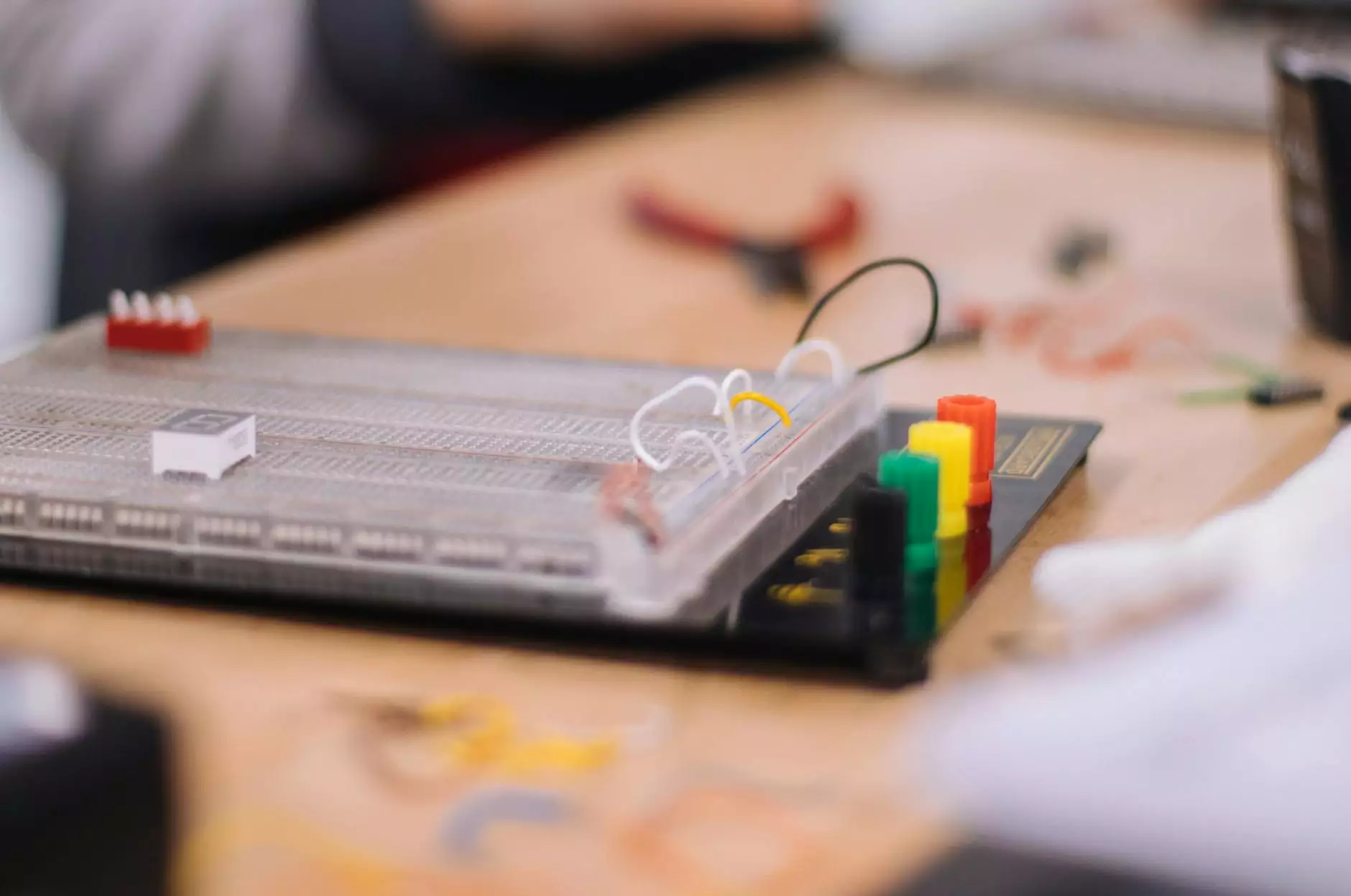
In today’s fast-paced manufacturing landscape, speed to market and product development agility are critical factors determining a company's competitive edge. Among the many technological advancements, rapid prototyping injection molding has emerged as a game-changer. This revolutionary process allows businesses to bring innovative ideas to life swiftly, fostering innovation, reducing costs, and streamlining the transition from concept to production.
Understanding Rapid Prototyping Injection Molding
Rapid prototyping injection molding is a specialized manufacturing technique that combines traditional injection molding processes with advanced rapid tooling methods. It enables the creation of highly detailed, functional prototypes and low-volume production parts in record time. Unlike conventional molding that often takes weeks or months to develop molds and fixtures, rapid prototyping injection molding can produce prototypes in days or weeks, directly impacting the overall product development cycle.
The Core Advantages of Rapid Prototyping Injection Molding
- Accelerated Development Cycle: Achieve faster iteration, testing, and validation of product concepts.
- Cost-Effective Short Runs: Significantly reduce initial tooling costs while maintaining high quality.
- Design Flexibility: Easily incorporate complex geometries and design variations without extensive retooling.
- High Precision and Quality: Produce prototypes that closely mimic final production parts in dimension, strength, and surface finish.
- Minimized Risks: Identify potential design flaws early, reducing costly modifications later in the production process.
The Technology Behind Rapid Prototyping Injection Molding
At the heart of rapid prototyping injection molding lies a fusion of innovative technologies:
- Rapid Tooling: Utilizes methods such as 3D printing, CNC machining, and electron beam melting to create swift, durable molds. These molds are suitable for low-volume production and testing.
- High-Quality Materials: Employs specialized plastics and metals that mimic final production materials' properties, providing realistic testing parameters.
- Precision Manufacturing Equipment: Advanced injection molding machines that deliver consistent, high-precision parts suited for functional testing.
DeepMould’s Expertise in Metal Fabrication for Prototyping
DeepMould, a leader in the metal fabricators industry, combines expertise in metal manufacturing with cutting-edge rapid prototyping methods. Our capabilities extend to:
- Custom Metal Prototypes: Rapidly produce metal components with complex geometries for testing and validation.
- Tooling and Fixture Fabrication: Design and manufacture specialized tooling that accelerates the prototyping process.
- Material Selection Guidance: Advise on the best metals for prototypes, considering strength, durability, and cost-efficiency.
- High-Precision Machining: Use machining techniques like CNC milling and EDM to achieve tight tolerances and intricate features.
How Rapid Prototyping Injection Molding Transforms Product Development
Incorporating rapid prototyping injection molding into your product development process can dramatically transform outcomes:
Fostering Innovation and Creativity
Quickly test multiple design iterations, making it easier to push creative boundaries and explore novel ideas without the constraints of traditional tooling delays.
Enhancing Collaboration and Communication
Prototypes serve as tangible representations of concepts, facilitating clearer communication among designers, engineers, marketers, and stakeholders, leading to more aligned decision-making.
Reducing Time-to-Market
By decreasing the time needed for prototype development and testing, companies can get their products into the marketplace faster, gaining a competitive advantage.
Lowering Development Costs
Early identification of potential issues prevents costly revisions and redesigns during later stages, significantly reducing overall project expenses.
Strategic Implementation of Rapid Prototyping Injection Molding
To fully leverage rapid prototyping injection molding, businesses should consider the following strategic steps:
- Define Clear Objectives: Ascertain whether the goal is functional testing, aesthetic validation, or low-volume production.
- Select Appropriate Materials: Choose plastics or metals compatible with your application and testing needs.
- Work with Expert Partners: Collaborate with experienced manufacturers like DeepMould who specialize in rapid prototyping and metal fabrication.
- Iterate and Refine: Use feedback from prototypes to refine designs, optimizing for manufacturability and performance.
- Plan for Transition to Production: Prepare for scaling up from prototypes to full-scale manufacturing once design validation is complete.
Why Choose DeepMould for Rapid Prototyping Injection Molding
DeepMould stands out in the industry for our comprehensive expertise in metal fabricators and advanced injection molding techniques. Our key strengths include:
- Innovative Technology Adoption: Utilizing the latest rapid tooling and manufacturing equipment to ensure quick turnaround times.
- Customized Solutions: Tailoring each project to meet specific design and functional requirements, ensuring optimal results.
- High-Quality Standards: Commitment to precision, durability, and surface finish, matching the standards of final production parts.
- Experienced Engineering Team: Skilled professionals dedicated to optimizing process flows, reducing costs, and ensuring accuracy.
- End-to-End Services: From initial design consultation through to prototype testing and low-volume production, we provide full-cycle support.
Future Trends in Rapid Prototyping Injection Molding
The landscape of rapid prototyping injection molding continues to evolve with technological advancements:
- Integration of Artificial Intelligence (AI): AI-driven design optimization and process control systems will further enhance efficiency and accuracy.
- Expanded Material Libraries: Development of new metals and plastics suitable for rapid tooling and prototype parts.
- Sustainable Manufacturing: Implementation of eco-friendly materials and processes to reduce environmental impact.
- Hybrid Manufacturing Techniques: Combining additive manufacturing with traditional injection molding for complex, multi-material prototypes.
Conclusion: Embrace the Power of Rapid Prototyping Injection Molding
In conclusion, rapid prototyping injection molding represents a transformative approach to product development that offers unparalleled speed, flexibility, and cost savings. By leveraging advanced technology and expert craftsmanship, companies can accelerate their innovation cycles, reduce risks, and bring high-quality products to market faster than ever before.
DeepMould is committed to providing leading-edge solutions in metal fabricators and rapid prototyping injection molding, empowering our clients to achieve their vision efficiently. Whether you are developing a new consumer product, a complex industrial component, or a cutting-edge technological device, our expertise ensures that your prototypes will meet the highest standards of precision, functionality, and reliability.
Invest in rapid prototyping injection molding today, and propel your business into a future of endless possibilities and accelerated growth.